If you're undertaking a retail or other commercial construction project, it's important to understand the…
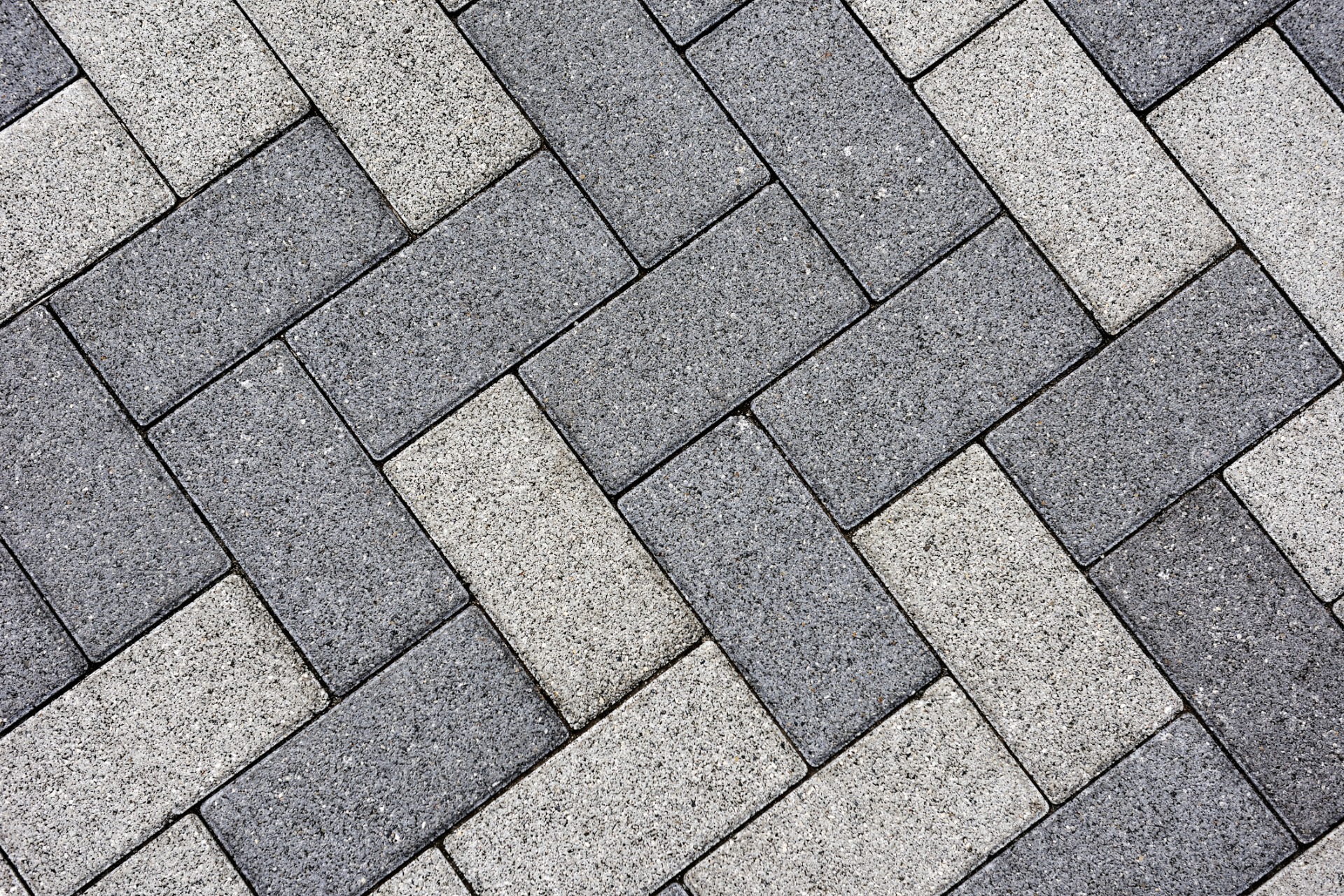
A Complete Guide to Commercial Concrete Maintenance
Even though concrete is a material known for its exceptional strength and durability, it can still wear down over time. Proper care and maintenance are crucial for keeping your commercial concrete surface in great shape. With a thorough understanding of the different issues that could affect your concrete, you’ll be well-prepared to address problems as they arise.
In this comprehensive guide, we’ll cover some of the most common maintenance concerns, including the following.
- Settling
- Rebar corrosion
- Alkali-silica reactions
- Freeze-thaw deterioration
- Surface maintenance
Let’s explore the causes and signs of each of these issues in more detail. We’ll also go over some helpful tips for prevention and repair.
1. Settling
Settling is one of the most common issues that commercial concrete surfaces face. Concrete settles when the ground beneath it shifts unevenly over time, causing it to sink or crack. There are a wide range of natural factors that can cause settling, including soil erosion, poor ground compaction, or fluctuations in moisture levels.
Signs of Concrete Settling
Concrete settling is usually hard to miss. Look for cracks, gaps, or potholes in the surface, as well as uneven or sloping surfaces.
Concrete Settling Prevention and Repair
The best way to prevent a commercial surface from settling is to properly prepare the site in advance. Settling often results from inadequate soil compaction before the surface is installed.
Once the concrete surface is in place, inspect it regularly for signs of settlement. If you do notice any signs, it’s crucial to act quickly. There are a few different ways to repair a settled surface.
One of the cheapest and most reliable methods is mudjacking. Mudjacking involves drilling holes in the surface of the concrete and hydraulically pumping a “mud” mixture underneath it, filling in the uneven gaps in the soil and lifting the surface back into a more even position.
Alternatively, polyjacking uses a lighter, longer-lasting, expandable polyurethane foam instead of a mud mixture.
The main downside of mudjacking and polyjacking is that, while both methods will re-level the surface, neither will make damaged concrete look better. If you want to restore the appearance of your commercial surface, you’ll also need to apply a cosmetic treatment like an epoxy covering.
2. Rebar Corrosion
Commercial concrete surfaces frequently have rebars underneath them to provide support. Over time, these rebars can corrode if they’re exposed to moisture, salt, or other corrosive substances.
Signs of Rebar Corrosion
It can be difficult to assess for rebar corrosion since the rebars are underneath the concrete and not easily visible to the naked eye. Watch out for crumbling, cracking, and rust stains along the surface.
Rebar Corrosion Prevention and Repair
Using corrosion-resistant rebars when you install your commercial concrete surface is the surest way to avoid corrosion later down the line. It’s also very important that the concrete over the rebars adheres to the minimum recommended cover thickness and that the rebars themselves are spaced appropriately with adequate distance between each bar.
Inspecting your concrete surface regularly and promptly sealing any cracks you find will help prevent moisture from seeping under the concrete and causing rebar corrosion.
3. Alkali-Silica Reactions
Alkali-silica reactivity (ASR) is a chemical reaction that occurs within concrete when certain aggregates react with the alkaline components in cement, producing alkali-silica gel over time. This gel can cause the concrete to expand and crack.
Signs of Alkali-Silica Reactions
The most common sign of ASR is the presence of thin, spidery cracks that spread randomly in all directions. These cracks are sometimes called map cracks or alligator cracks because they cause the surface to resemble an old map or an alligator’s skin.
ASR Prevention and Repair
The surest way to prevent ASR is to use low-alkali cement for your commercial cement surface. Minimizing moisture penetration by keeping cracks and joints sealed can also help to slow the expansive effects of alkali-silica reactivity. If the problem is already severe, replacing the concrete may be your only option.
4. Freeze-Thaw Deterioration
Freeze-thaw deterioration occurs when water enters a concrete surface, then freezes and expands, leading to internal pressure that weakens and cracks the concrete. This is often a major issue in regions with cold climates or harsh winters.
Signs of Freeze-Thaw Deterioration
Some of the most common signs of freeze-thaw deterioration are flaking, pitting, or spalling on the surface, which leaves it noticeably rough-looking. You may also begin to spot cracking or even large chunks breaking free from the concrete surface, leaving visible scarring.
Freeze-Thaw Deterioration Prevention and Repair
The most important element in preventing freeze-thaw deterioration is properly mixed concrete. Commercial concrete surfaces in climates where freeze-thaw deterioration is a risk should always be laid with concrete that contains entrained air. Air entrainment is a mixing technique that involves intentionally injecting microscopic air bubbles into the concrete to accommodate the expansion that happens when water inside the concrete freezes.
Of course, thoroughly sealing your concrete surface to prevent moisture from entering in the first place can also help minimize the effects of the freeze-thaw cycle.
5. Surface Maintenance
Aside from structural issues that affect the strength and function of your commercial concrete surface, there are also surface maintenance issues to consider. Surface maintenance is essential for maintaining a clean and safe commercial environment. Dirty or damaged surfaces can cause trips, slips, falls, and other accidents that are better avoided.
Surface Maintenance Tips
Regularly sweep surfaces where people walk or stand to minimize the risk of slips. Periodically pressure washing your commercial concrete surface can also help to combat stubborn grime that builds up over time. Most importantly, make sure you promptly repair any minor surface damage like cracks or holes that could become tripping hazards.
Commercial Concrete Maintenance Services
Keeping your commercial surface clean and addressing minor issues may be something you can handle by yourself, but major issues like settling or ASR are often best left to a professional. Keep a close eye on the condition of your concrete and contact K&E Flatwork if you notice any of the issues we mentioned in this list. Whether you need a routine repair or a full replacement, K&E has you covered.