If you own or manage a commercial property, you know how important it is to…
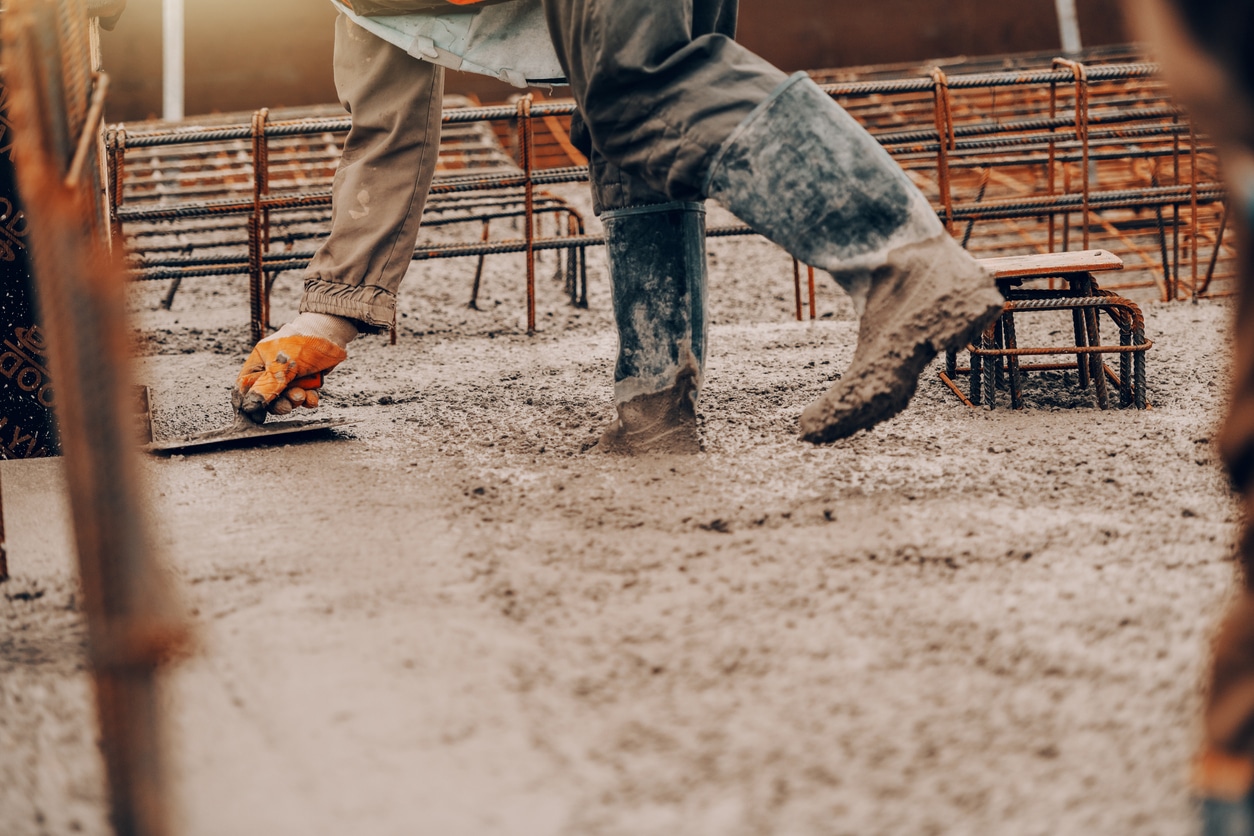
10 Common Concrete Problems and How to Solve Them
Concrete is a ubiquitous material used in both commercial and residential construction due to its durability, versatility, and cost-effectiveness. However, like any other building material, concrete is not immune to problems that can arise over time.
In this article, we’ll explore ten of the most common concrete problems we see and provide effective solutions for each one. Whether you’re a property manager, business owner, or facilities maintenance professional, this guide will equip you with the knowledge needed to address commercial concrete damage promptly and effectively. From cracks and spalling to discoloration and scaling, we’ve got you covered.
Continue reading below to learn more and discover why K&E Flatwork is the number one choice for commercial concrete services in Kansas City.
Navigating Common Concrete Issues
Understanding common concrete problems and their effective solutions is key to ensuring the longevity and aesthetic appeal of your concrete. Let’s explore some of these challenges and provide practical, expert-guided solutions to keep your concrete in top condition.
Cracks
One of the most prevalent issues with concrete is cracking. Understanding the different types of cracks can help identify their underlying causes and determine appropriate repair methods.
Plastic Shrinkage Cracks: These cracks occur during the curing process when rapid moisture loss causes the surface to shrink.
Drying Shrinkage Cracks: As the concrete dries and loses moisture over time, it undergoes shrinkage, resulting in these cracks.
Settlement Cracks: Uneven soil settling beneath the structure can cause these cracks.
Structural Cracks: These are typically caused by excessive loads or foundation movement.
To effectively repair cracked concrete, it’s crucial to assess the type of crack first. For small hairline cracks or surface cracks, simple patching compounds or epoxy fillers may suffice. However, larger or structural cracks might require more extensive measures such as crack injection or full-depth repairs.
Spalling
Spalling refers to the chipping or flaking off of a concrete surface layer. It not only compromises the overall aesthetics of the concrete surface but also exposes the underlying layers to moisture penetration and further damage. Understanding its causes can help address this issue effectively.
Freeze-Thaw Cycle: Exposure to repeated freezing and thawing can cause water to expand and contract within the concrete, leading to spalling.
Chemical Damage: Certain chemicals, such as de-icing agents or chloride-based compounds, can penetrate the concrete surface and contribute to spalling.
To repair spalled concrete, start by removing the damaged portions and cleaning the area thoroughly. Then, apply a bonding agent and use a suitable patching material to restore the surface. In cases of significant damage, resurfacing the entire area may be necessary.
Scaling
Scaling refers to the flaking or peeling away of thin layers from the surface of hardened concrete. This commonly occurs due to freeze-thaw cycles, poor finishing techniques, or inadequate curing processes. To restore your concrete’s natural beauty:
Remove Loose Material: Start by removing any loose debris or scaling using a wire brush or power washer.
Repair Surface Imperfections: Fill in any pitted areas with a repair mortar mix.
Seal and Protect: Apply an appropriate sealer or coating to protect against future scaling and enhance durability.
Proper maintenance practices such as regular sealing and avoiding harsh de-icing chemicals can help prevent scaling in the long run.
Discoloration
Concrete discoloration can result from various factors, including improper mixing, insufficient curing time, exposure to certain chemicals, or environmental conditions. Here are some methods for addressing discoloration issues:
Cleaning Agents: Utilize mild cleaning agents like trisodium phosphate (TSP) or specialized concrete cleaners to remove stains caused by oil spills, rust, or organic matter.
Acid Stain Removal: In cases where acids have caused discoloration, acid etching might be necessary, followed by neutralization and thorough rinsing.
Surface Overlays: If all else fails, adding a decorative overlay can provide a fresh look to discolored concrete surfaces.
Remember, prevention is the best approach. Avoid using incompatible materials or chemicals that could potentially cause discoloration.
Crazing
Crazing refers to the fine network of cracks that often resemble a spider web on the concrete surface. These cracks are typically shallow and do not extend through the entire thickness of the concrete. Here’s how you can address this aesthetic concern:
- Thoroughly clean the crazed area by removing any dirt or debris.
- Apply a thin overlay or microtopping to even out the surface and minimize the visibility of crazing.
Regular maintenance and avoiding excessive moisture can help prevent further crazing on your concrete surfaces.
Efflorescence
Efflorescence is a common issue in concrete, where a white powdery substance appears on the surface. This is often caused by excess water in the concrete mix, water seeping into the concrete from the ground, or rain or heavy dew in outdoor environments. When the water evaporates, these salts are left behind, creating an unsightly white deposit.
Addressing efflorescence requires several steps:
- Use a mild acid or specialty cleaner to remove the efflorescence. Always follow the manufacturer’s instructions and ensure that you rinse thoroughly to avoid acid etching.
- Once clean, apply a high-quality sealer to the concrete surface. This will help to block pores and prevent water from seeping into the concrete.
- Proper drainage systems should be in place to prevent water accumulation. In indoor settings, consider using dehumidifiers.
Remember, the key to preventing efflorescence is to limit the movement of water through the concrete. Always ensure proper sealing and moisture control in your concrete installations.
Curling
Curling is a condition observed in concrete slabs where the edges of the slab tend to rise or “curl” due to differential shrinkage. Curling is most often caused by a gradient in moisture content or temperature between the top and bottom surfaces of concrete slabs. For instance, the top surface of the slab often dries more rapidly than the bottom, leading to a higher degree of shrinkage at the surface and thus triggering curling.
To prevent curling, consider the following:
- Implement a curing regimen to ensure uniform drying. Keep the slab moist for a sufficient period after placing the concrete, using curing blankets or other moisture-retaining methods.
- Install control joints at regular intervals to allow for some degree of shrinkage without causing curling.
Remember, the key to preventing curling lies in a balanced approach that considers the mix of design, placement, and curing, as well as climate conditions during and after construction.
Blistering
Blistering is another common defect encountered in concrete surfaces, characterized by small, raised, hollow bumps on the concrete surface. Some of the leading causes of blistering include delayed finishing, insufficient venting, or incorrect concrete mix. Preventing blistering involves several measures, such as:
- Ensure that finishing operations begin once the bleed water has evaporated from the surface. This helps to avoid trapping air or bleed water beneath the finished surface.
- Follow the recommended mix proportions. Too much cement or fine aggregates can lead to a dense mix that traps air and leads to blistering.
Appropriate Venting: Use a roller during the finishing operations. This can help to push out any trapped air, preventing the formation of blisters.
By taking these precautions, blistering can be avoided, resulting in a smooth and quality concrete surface.
Delamination
Delamination is a defect that manifests as a separation along the plane of a concrete slab, resulting in a thin, horizontal layer peeling away from the primary surface. This condition often remains hidden under the surface and may not be readily visible, making it a particularly challenging issue to diagnose and address. Some of the leading causes of delamination include rapid drying, overworking of the surface, and non-uniform distribution of the concrete mix.
Mitigating delamination involves adopting the correct practices at various stages of concrete handling:
- Ensure that curing conditions maintain adequate moisture levels, preventing rapid drying that can lead to delamination.
- Avoid overworking the surface and ensure finishing operations only commence once the bleed water has evaporated.
- Ensure a uniform distribution of aggregates to avoid creating a weak layer that can delaminate.
Through diligent application of these strategies, the risk of delamination can be significantly reduced, contributing to a robust and long-lasting concrete structure.
High Permeability
Permeability in concrete refers to the degree to which water and air can pass through the material. High permeability can lead to a variety of structural issues, including corrosion, freeze-thaw damage, and decreased durability. Several factors can contribute to increased permeability in concrete, including insufficient curing, concrete mix with an excessive water-cement ratio, and over-vibration during the placement stage.
Addressing permeability issues requires both preventative and remedial actions:
- Ensure the concrete is adequately cured to reduce the porosity of the surface and lower permeability.
- Maintain an appropriate water-cement ratio in the concrete mix to reduce porosity.
- Avoid practices like over-vibration that can lead to segregation and increased permeability.
Paying close attention to these aspects can significantly reduce the permeability of concrete, enhancing the lifespan and durability of the structure.
Choose K&E Flatwork for Your Commercial Concrete Needs
Concrete problems can be a headache for all commercial property owners. However, with knowledge about common concrete issues and their solutions, you can tackle these challenges head-on. By taking proactive measures and implementing appropriate concrete repair solutions when needed, you can ensure that your concrete remains strong, durable, and visually appealing for years to come.
Are you looking for top-tier commercial concrete solutions in Kansas City? At K&E Flatwork, we understand the complexities of concrete projects and bring a blend of quality, efficiency, and dedication to every job. From expansive warehouse floors to intricate loading docks, our wide-ranging expertise ensures that your project is handled with utmost professionalism.
If you’re looking for a concrete repair team that values timely delivery, transparent pricing, and exceptional workmanship, K&E Flatwork is your go-to choice. Contact us today to learn more about our commercial concrete services and find out how we can make a difference in your next project with our expertise and commitment to excellence.